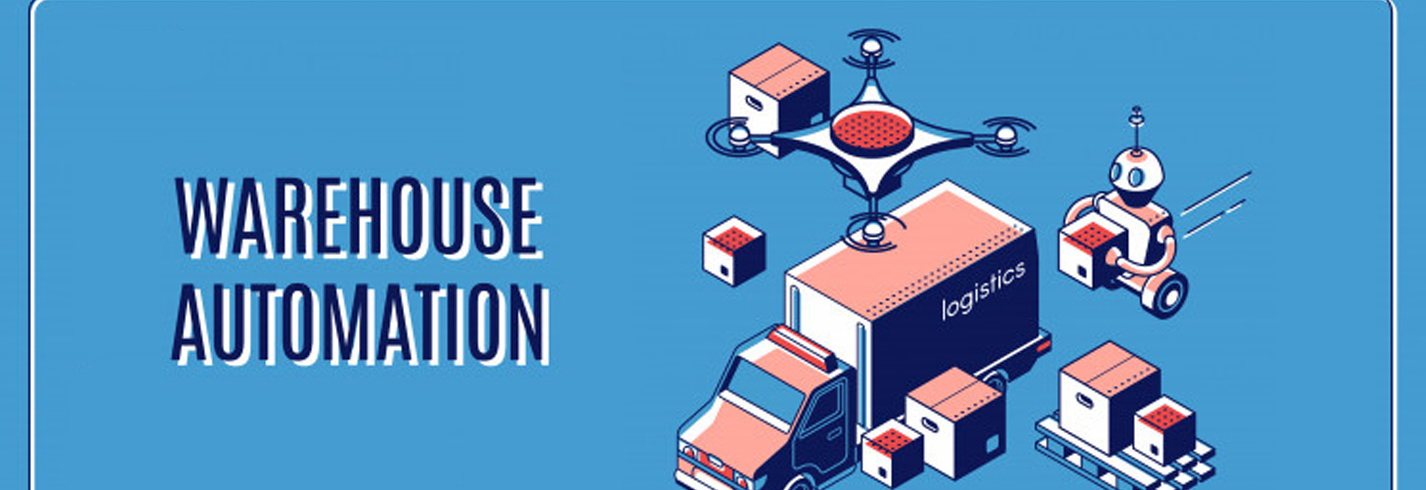
Warehouse Automation
Warehouse Automation
Gone are the days of thinking that paper-based processes are enough for warehouses. Automation in warehouses has advanced over a couple of decades- right from the deployment of sortation systems to automatic conveyors, Automated Guided Vehicle (AGV) to RFID systems and complex warehouse management systems (WMS). Automation in the warehouse is largely used to make improvements in current processes by improving speed, accuracy, consistency, efficiency, and ultimately cost savings. Now organisations are profoundly investing in automation and robotics in their warehouses. For instance, Amazon recently started deploying warehouse robots called Kiva robots which do picking and put away in the warehouse. These sensor-based robots avert accidents and algorithms aid in the decision-making the process. To eliminate repetitive, process-based, and error-prone tasks in warehouses, we have multiple options of automation to make operations fool-proof:
Picking automation –
The manual picking process is a highly repetitive & time-consuming which increases the likelihood of human error. Today’s modular shelving system in conjunction with warehouse robots makes picking process error-free.
Barcode labels and scanning automation –
Warehouses are dependent on documentation for in and out the movement of products. Companies can save a huge number of man-hours by automating the paper-based processes through rack labels, barcode labels, and scanners. Not only this kind of automation eliminate errors but also increases the speed up documentation process.
Automated vehicles –
Long gone when forklifts and pallet trucks were used to move goods in the warehouses. Now thanks to AGVs which are automating multiple processes in the warehouses as track digital pathways through the facility to load and unload pallets and do not require human intervention.
AS-RS-
It is a fixed aisle Automated storage and retrieval system that moves pallets in and out of storage locations. These systems not only offer reduced space but are also consistent and safe for product handling.
Inventory automation –
Inventory cycle counts are prone to data entry errors and inconsistent inventory processing. Carrying out inventory count through camera-mounted drones and automating inventory management through WMS is one of the easiest and cost-saving approaches warehouses can implement to start realising the benefits of automation
Back-office automation –
Warehouses that don’t have access to real-time data in their WMS results inaccurate inventory counts – which can cause supply chain disruptions. In ever-changing logistics and warehousing industry, having accurate, precise and real-time data is crucial which makes WMS indispensable in today’s world.
Implementing automation in warehouse resolves a lot of issues for companies:
- Trim labour costs and quicker return on investment over the long term – ranging from cutting manpower costs by 80% and operating costs by 20%
- Solves the problem of labour scarcity during peak season and shift shuffling
- Eliminates the risk of injuries and accidents
- Maximises space utilisation by decreasing warehouse area up to 40%
Regardless of the advantages, warehouse automation has certain disadvantages:
- Hefty investment of $40-$100 million- depending on the size and complexity of the operations.
- Automation is mostly inflexible- Humans are more flexible to evolving business needs.
- Eliminates the risk of injuries and accidents
- Maximises space utilisation by decreasing warehouse area up to 40%
Despite disadvantages, warehouse automation is the need of the hour and should be done with due diligence considering the following factors in mind such as:
- Creating a logistics model aligned with strategic objectives of the organisation and operations strategy
- Comprehending the maturity, complexity, manpower issues, existing technology in operations
- Carrying out thorough operational analysis through optimisation and simulation tools to calculating cost per unit, the cost to serve, return on investment and benchmark against the best in industry
The top-of-mind attention for management is on Four-wall savings, but these savings are not the only added value of automation. Warehouse automation has a broader supply-chain impact through network benefits and strategic advantages. In short, the potential benefit of warehouse automation is realised across the entire supply chain network. The companies must play on their competencies in the supply chain since there is already huge pressure to reduce costs and fulfil orders. I believe, the organisations that will make a mark in the future will be those that can capitalise on the next-gen warehouse automation and are flexible enough to take advantage of new technologies.
Disclaimer: Views expressed here are the author’s personal views.