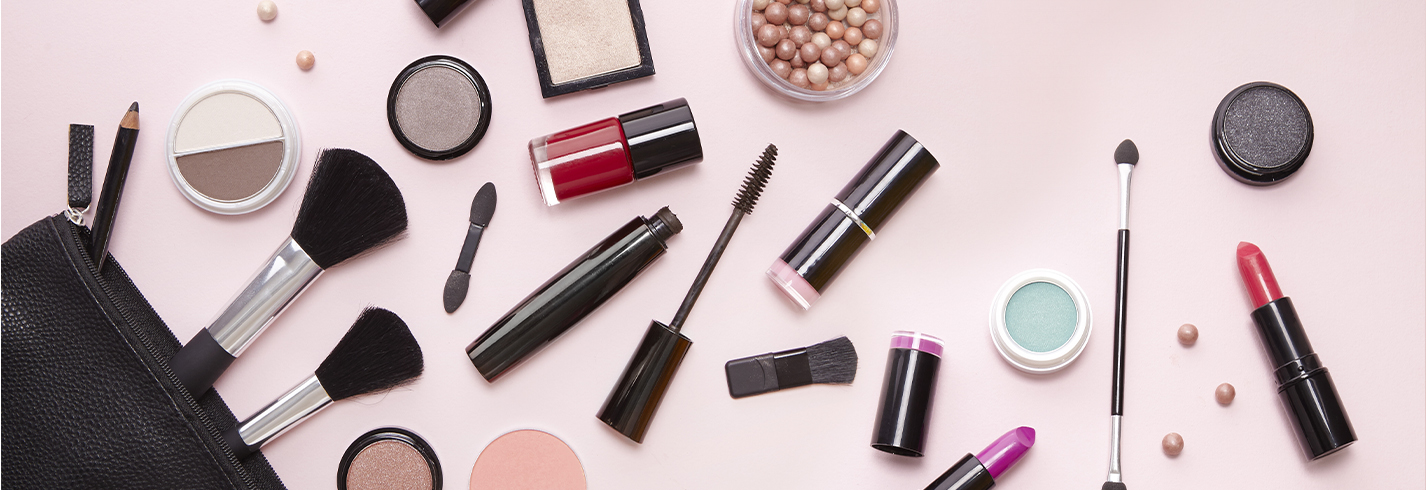
Delivered the Glow of Success: Achieved 100% Inventory Accuracy and 50% Reduction in Vehicle Detention for a Leading Indian Cosmetic Brand
The cosmetics and beauty sector in India has grown significantly in recent years, driven by shifting consumer habits and heightened awareness of personal grooming and beauty trends. This vibrant market boasts a wide array of offerings, spanning skincare, haircare, makeup, fragrances, and personal hygiene products, addressing the evolving preferences of consumers from various demographic backgrounds. Given the diverse range of cosmetic products, efficient transportation and distribution are crucial to ensure timely availability and meet consumer demand.
Our customer, a well-known Indian cosmetics and beauty brand under a large multinational FMCG conglomerate, offers a wide range of beauty and skincare products, including makeup, skincare, and haircare items. The two major focus areas for our customer were to optimise warehouse space and reduce the rate of vehicle detention.
Optimising FMCG Supply Chain With Our Integrated Warehousing and Distribution Solutions
With our integrated warehousing and distribution solutions, we manage long-span rack (LSR) and block storage systems for over 960 SKUs across various product categories. Additionally, we have established an omnichannel distribution network capable of handling a volume of 20,000 standard throughput/day and 22,140 throughput/day during peak seasons.
Warehouse Space Optimisation: We installed long-span shelving racks to manage a wide range of SKUs, ensuring high inventory accuracy and efficient storage handling. To optimize storage utilization, non-moving products identified through aging reports were regularly relocated to other warehouses.
Temperature-Controlled Storage: Our state-of-the-art warehouse is equipped with cold storage systems designed to maintain temperatures within a specific range. We ensured that the temperature of specific product categories remains between 22 and 27 degrees Celsius to preserve the quality and integrity of the products.
Automation Initiatives: As part of our commitment to operations excellence, we’ve introduced picker trolleys, streamlining processes, and boosting productivity in warehousing operations. Additionally, these automation initiatives not only expedite order fulfilment but also enhance accuracy, ensuring customer satisfaction remains at the forefront of our operations, all while optimizing costs.
Diverse Workforce: At the heart of our operations lies our commitment to diversity and inclusion, with women comprising 60% of our team at this location. We actively foster an inclusive workplace culture that celebrates diversity in all its forms, ensuring equal opportunities for growth and advancement for all employees, regardless of gender, ethnicity, or background.
Value Added Services: In addition to order consolidation, packing, and tagging, we also offer quality assurance checks and customizable packaging solutions tailored to our clients’ specific requirements, ensuring that each product is delivered to our customers with the utmost care and attention to detail.
Igniting Success: Driving Accuracy and Cost Optimisation
- 100% inventory accuracy
- 50% reduction in vehicle detention
- ZERO handling damages
- Improved on-time delivery from 96% to 99.6%
- 99.5% dispatch accuracy
- 99.5% order fulfilment
Harnessing our industry experience and strategic insights, we’ve not only met but exceeded the evolving demands of the market. By optimizing operations and cultivating a diverse workforce, we’re Igniting Success for our customer, delivering exceptional service, and driving growth in the competitive FMCG landscape.