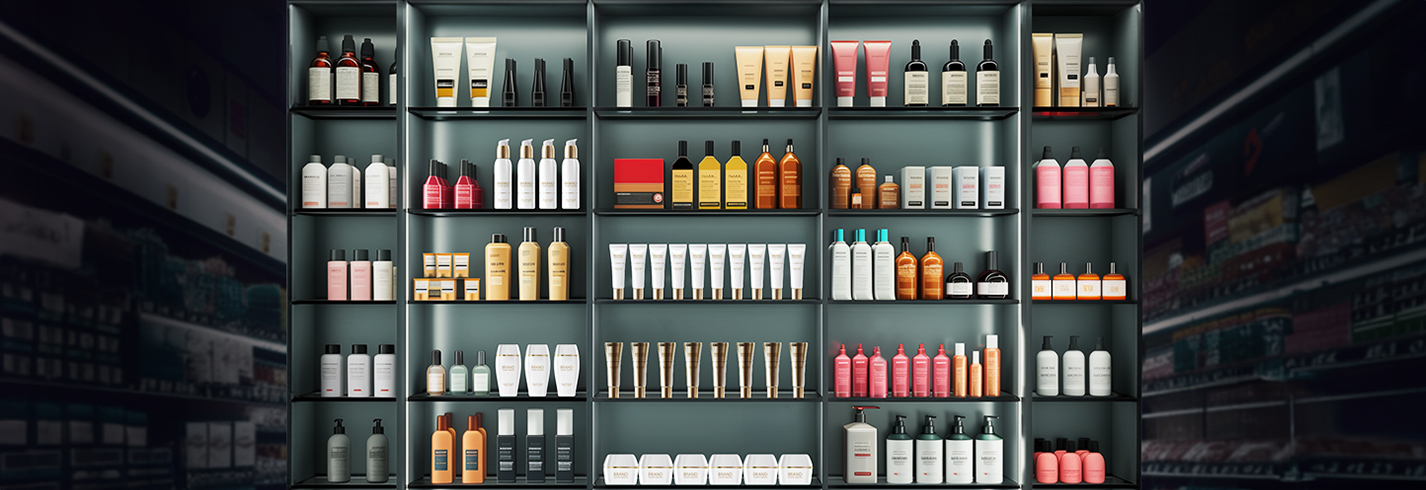
Igniting Success with 99.9% Inventory Fill Rate For A Leading French Cosmetic Company
The cosmetics industry’s rapid expansion is driven by growing consumer spending power and ever-changing preferences. With a diverse array of product categories to cater to varied tastes, both domestic and international brands compete for attention in this competitive landscape. The advent of e-commerce has revolutionized accessibility, allowing consumers from all walks of life to explore and purchase products conveniently online. Within this context, logistics emerges as a cornerstone, facilitating prompt order fulfilment and robust reverse logistics mechanisms essential for ensuring customer satisfaction and fostering brand loyalty in an industry where customer-centricity reigns supreme.
Our customer, a leading French personal care and cosmetics brand with product categories spanning hair care, skin care, sun protection, makeup, and perfumes, was focused on improving same-day order processing, addressing continuous volume fluctuations, and effectively managing returns volumes.
Streamlining Cosmetics Warehouse Operations Through Our Warehousing Solutions
Serving Delhi NCR, UP, and Haryana regions, our state-of-the-art warehousing solutions feature HDD racks with 6003 pallet positions and 3350 shelving locations, ensuring efficient utilization of space. Providing end-to-end warehousing solutions, we manage a throughput of 3.9 lakh per month and handle a throughput of 4.8 lakh per month during peak seasons.
Inventory Management: We conducted regular SKU bin consolidation to maximize bin usage, particularly for small quantity SKUs, ensuring efficient space utilization. Daily tracking and management information system (MIS) were implemented for promotional items orders, facilitating timely and accurate inventory management. In line with our commitment to swift operations, all unloaded materials were inventoried within 24 hours of arrival, enhancing accuracy and minimizing discrepancies. Meticulous attention was given to the picking and packaging of loose products, ensuring precision and efficiency in order fulfilment processes.
Automation Initiatives: One of the notable initiatives in progress is the implementation of robotic picking technology aimed at enhancing picking accuracy while realizing substantial cost savings in workforce expenditure. By introducing robotics into our picking processes, we anticipate not only improved efficiency but also reduced errors, leading to enhanced customer satisfaction.
Workforce Management: We prioritized versatility and skill enhancement among our employees through regular cross-deployment, fostering adaptability across various roles.
Additionally, we invested in boosting morale and providing ongoing upskilling opportunities to retain our skilled workforce. With a current diversity rate of 29%, we are committed to further improving inclusivity at our site.
Sustainability Initiatives: The warehousing facility is part of a multi-client warehousing and distribution network. Within this setup, we have deployed solar power panels, electric bikes with dedicated charging stations for internal warehouse movement, installed sensors to monitor air quality, and established a sewage treatment plant.
Igniting Success: Driving Inventory Accuracy
- Improved inventory fill rate from 98% to 99.9%
- 100% same day unload to inventory
- 100% same day order processing and dispatch
- Achieved overall SLA of 98.5%